似島グランピング施設における高所作業車を用いた高木危険伐採事例
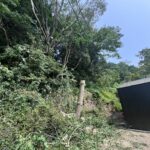
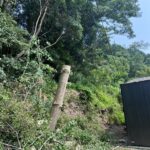
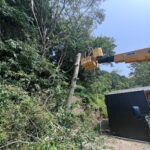

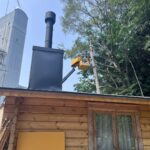
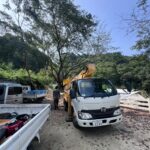
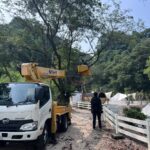
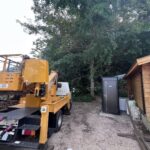
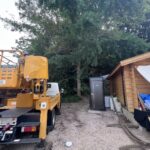
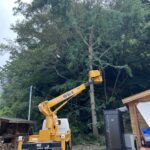
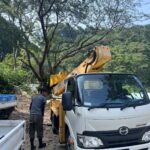
目次
- はじめに
- 事例概要
- 依頼背景と現地条件
- 作業計画・工程立案
- 使用機材・装備一覧
- 施工手順
6.1 下部枝払いと搬出ルート確保
6.2 高所作業車によるセクション伐採
6.3 ロープワークによる落下制御
6.4 幹の玉切り・搬出 - 安全対策・リスクマネジメント
7.1 電線・施設への配慮
7.2 作業員のPPEと動線管理
7.3 アウトリガー設営と地盤対策 - 施工後の整地・片付け
- 結果と効果検証
- 振り返りと今後の改善ポイント
1. はじめに
似島の豊かな自然環境は、グランピング施設の魅力を大きく引き立てますが、同時に管理が難しい高木や枯損木が放置されると、強風時や積雪時に倒木・落枝の危険を高めます。本事例では、施設利用者の安全確保と周辺設備への影響を最小限に抑えるため、高所作業車とロープワークを組み合わせたセクション伐採を実施しました。以下では、依頼背景から施工手順、安全対策、施工後の効果検証までを体系的にまとめています。
2. 事例概要
- 場所:広島湾に浮かぶ似島内グランピング施設敷地内
- 対象樹木:シラカシ(推定樹高約12m、幹直径約40cm、施設入口脇に位置)
- 目的:枯損・樹勢不良による倒木リスクの除去と、施設利用者・設備への安全確保
- 作業期間:1日(作業時間:約6時間)
- 作業人数:3名(高所作業車オペレーター1名、伐採作業員1名、地上誘導員1名)
- 使用機材:高所作業車(作業床耐荷重200kg、最大作業高約10m)、25cc チェーンソー、スリングロープ、ウエハ(アウトリガー底板)
- 天候条件:晴天・微風(風速2m/s以下)
本事例では、限られたスペースと宿泊施設の周辺設備を考慮しつつ、セクションごとに幹と枝を落として安全に搬出しました。次節以降で、依頼背景や施工手順、安全対策などを詳述します。
3. 依頼背景と現地条件
3.1 依頼背景
似島グランピング施設は、山裾の豊かな緑に囲まれた立地を活かし、多くの宿泊客が自然を満喫しています。しかし敷地入口脇に立つシラカシの大木は、樹齢とともに幹の一部に枯損が見られ、強風時や積雪時に倒木・落枝の危険性が増していました。特にバンガロー棟への動線上に位置しているため、利用者の安全確保と施設設備への被害防止を目的に伐採のご依頼をいただきました。
3.2 現地条件
- 地形・アクセス
山の中腹に位置し、西側が急傾斜の雑木林、東側に宿泊用小屋や薪棚、仮設トイレ棟が立ち並ぶ狭隘地。作業車両は約2tの高所作業車一台のみ進入可能で、アウトリガー展開のためのスペース確保が求められました。 - 地盤・設営条件
敷地は砂礫混じりの緩い土質。アウトリガー底板(ウエハ)を使用して荷重を分散し、バケット車の安定設営を図る必要がありました。 - 周辺障害物
・電線(高所作業エリアの真横を通過)
・小屋の換気塔や薪置き場
・白い木製フェンスとゲスト動線 - 気象条件
当日は晴天・熱中症リスクにも配慮し、風速2m/s以下の微風でチェーンソー作業に支障のない好条件でした。
これらの条件を踏まえ、限られた作業スペースと周辺設備への影響を最小限に抑えながら、安全第一で施工計画を立てました。次節では、具体的な作業計画と工程立案の詳細を解説します。
4. 作業計画・工程立案
4.1 施工フローの全体像
- 事前現場調査
- 樹高・樹勢の再確認、作業半径と落下ゾーンのマーキング
- 高所作業車の進入経路とアウトリガー設置箇所の確認
- 安全ミーティング
- 作業手順と役割分担(オペレーター/伐採作業員/地上誘導)の共有
- 緊急時連絡方法・避難経路の確認
- 機材設営
- アウトリガーをウエハ(底板)設置で水平かつ沈下対策
- チェーンソー・ロープ類・PPEの最終点検
- 伐採工程
- 下部枝払い → 高所進入 → 捨てロープ設置 → 受け口・追い口カット → 地上引き降ろし
- 各セクションごとに工程写真撮影と作業記録
- 搬出・片付け
- 伐採材を玉切り → トラック積載場所へ運搬
- 作業エリアの清掃と最終安全確認
4.2 役割分担
- 高所作業車オペレーター:バケットの位置決め、安全確認と緊急停止判断
- 伐採作業員:チェーンソーによる切断、ロープワークによる吊り降ろし操作
- 地上誘導員:落下ゾーンの監視、ロープ引き、周囲への注意喚起
4.3 工程ごとの所要時間見積もり
工程 | 担当 | 時間目安 |
---|---|---|
現場調査・マーキング | 全員 | 30分 |
安全ミーティング | 全員 | 15分 |
機材設営 | オペレーター | 30分 |
下部枝払い | 伐採作業員 | 45分 |
高所進入・ロープ設置 | オペレーター+伐採作業員 | 30分 |
セクション伐採(×4区画) | 伐採作業員+地上誘導員 | 各45分 |
搬出・片付け | 全員 | 60分 |
合計(休憩含まず) | 約5時間 |
4.4 コミュニケーション手段
- ヘルメット内蔵無線機で常時連絡を維持
- 地上誘導員はホイッスルとハンドシグナルも併用
これらの計画をもとに、安全かつ効率的な作業を実現しました。次節では、実際に投入した機材・装備の詳細を紹介します。
5. 使用機材・装備一覧
項目 | 仕様・用途 |
---|---|
高所作業車 | - 型式:バケット車(最大作業高10m、作業床耐荷重200kg) - アウトリガー4脚式、水平・沈下防止のためウエハ併用 |
チェーンソー | - 排気量:25ccクラス - ガイドバー長さ:35cm(切断精度と取り回しのバランス重視) |
スリングロープ | - タイプ:ダイニーマ/ポリエステル混紡 - 耐荷重:5t以上 - 切り落とすセクション毎に巻き付け、吊り降ろしに使用 |
捨てロープ(コントロールロープ) | - 長さ:20m前後 - 用途:枝・幹の落下方向を制御し、安全に引き降ろす |
アウトリガー底板(ウエハ) | - サイズ:30×30cm以上の鋼製または樹脂製プレート - 用途:地盤への沈下を防ぎ、車両安定化 |
個人保護具(PPE) | - ヘルメット(あご紐・フェイスシールド付) - 安全帯(フルハーネス型、ランヤード付) - 防振手袋、耐切創ズボン - 安全靴(つま先鋼製) |
コミュニケーション機器 | - ヘルメット内蔵無線機(双方向通話) - ホイッスル・ハンドシグナル |
その他工具・消耗品 | - 携帯ノコギリ・小型ノコギリ - カラビナ・シャックル各種 - マーカー・フラッグ(作業区域マーキング用) |
各装備は、事前に可動・摩耗点検を行い、予備ロープや替え工具も必ず現場に待機させました。次節では、これらを用いた具体的な施工手順を詳細に解説します。
6. 施工手順
6.1 下部枝払いと搬出ルート確保
- 地上からの枝払い
- 地上作業員がチェーンソーを用い、手の届く範囲の細枝・小枝を払って視界・作業スペースを確保。
- 枝くずは仮置き場にまとめ、作業床への落下物を最小限に抑える。
- 搬出ルートのマーキング
- 玉切り後の幹・枝を搬出するルートを、フラッグやマーキングテープで明示。
- ルート上に障害物(石・根株・資材)がないか最終確認し、必要に応じて軽く除去。
6.2 高所作業車によるセクション伐採
- バケット車進入・アウトリガー展開
- 事前に決めた設置位置へゆっくり進入し、ウエハを介してアウトリガーを水平に張出。
- 作業床上昇・ポジショニング
- 作業員がバケットに乗り込み、狙う枝元または幹のセクションに合わせて高さ・角度を微調整。
- 受け口・追い口のマーキング
- 切断面を受け口(下側)と追い口(上側)で位置取りし、チェーンソーの切り込み線を養生テープ等で可視化。
6.3 ロープワークによる落下制御
- 捨てロープの取り付け
- 切断予定セクションにスリングロープを巻き付け、カラビナでバケット端に仮固定。
- 地上誘導との連携
- 地上で待機する誘導員がロープを軽く引き、落下方向と速度をコントロールできる状態に。
- 安全確認後のカット
- オペレーターと伐採作業員が無線で「カットOK」を合図し、受け口→追い口の順で丁寧に切断。
- 落下の制御
- セクションが外れたら、地上でロープを引き落として着地衝撃を緩和。暴れや跳ね返りを防ぐ。
6.4 幹の玉切り・搬出
- 玉切り寸法の指示
- 搬出しやすい長さ(約50cm)に地上誘導員が寸法を指示。チェーンソーで玉切り。
- 仮置き場への積み上げ
- 玉切り材は仮置き場に整然と並べ、搬出トラックへの積み込み準備と動線確保。
- 最終確認
- 作業エリアに残留物(小切れ片・木くず)がないか最終チェックし、安全柵・マーキングを撤去。
以上の手順を経て、限られたスペースでも安全・効率的に高木の危険伐採を完遂しました。次節では、安全対策とリスクマネジメントについて詳述します。
7. 安全対策・リスクマネジメント
7.1 電線・施設への配慮
- クリアランス確保:バケットやロープ、落下する木片が電線に触れないよう、事前に最小クリアランス(1.5m以上)を計測し、マーキング。
- 接近警告:電線近くの作業時は「電線接近警告表示板」を設置し、常時目視で監視。オペレーターには電線距離アラーム付きセンサーを装備。
- 施設保全:動線上にある小屋・フェンス・薪棚などへの飛散防止のため、飛散防護ネットを仮設。また、小屋換気塔周囲にはバリケードを置いて直接衝突を回避。
7.2 作業員のPPE と動線管理
- PPEの徹底着用:ヘルメット+フェイスシールド、防振グローブ、安全帯(フルハーネス)、耐切創ズボン、安全靴は必須。
- 立入禁止ゾーンの設定:伐採エリア周囲にカラーコーンやバリケードテープで「立入禁止ライン」を設置し、作業外のスタッフや利用者を締め出す。
- コミュニケーション:無線とホイッスル、ハンドシグナルを併用し、常に地上誘導員とオペレーター間の意思疎通を維持。緊急停止コマンドは全員で共通運用。
7.3 アウトリガー設営と地盤対策
- 支持基盤の強化:緩い砂礫地盤では、ウエハ(底板)だけでなく、追加の「地盤支持マット」を使用し、アウトリガー荷重を広く分散。
- 水平確認:設置後に水準器で前後左右の水平を確認。必要に応じて微調整し、左右のアンバランスによる転倒リスクを低減。
- 沈下監視:作業開始後も定期的にアウトリガー周囲の沈下を目視点検し、異常があれば速やかに作業中断・再設営。
以上のリスクマネジメントを徹底することで、設備・周辺環境への影響を最小限に抑えつつ、作業員の安全を確保しました。次節では、施工後の整地・片付けについてご説明します。
8. 施工後の整地・片付け
- 伐採材の整理・搬出準備
- 玉切り済みの幹・枝を長さや太さ別に分類し、トラック積載時の効率を高める配置で仮置き場に整列。
- チェーンソーオイルや潤滑剤が漏れた箇所は吸着マットで回収し、土壌汚染を防止。
- 現場清掃
- 小切れ片や木くずを熊手・ブラシで集め、専用容器に回収。
- 足元の滑りリスクを排除するため、作業エリアは高圧洗浄機またはホース水洗いで清掃。
- マーキング・バリケードの撤去
- 立入禁止テープ、フラッグ、カラーコーンをすべて回収し、元の状態に復旧。
- 飛散防護ネットや仮設バリケードも撤去し、施設内通路の視認性を確保。
- 設備・地面の最終点検
- フェンスや小屋の壁面、床面に傷やへこみがないかをチェック。必要があれば補修または清掃。
- 地盤に沈下や不陸が残っていないか確認し、凹凸があれば砂利や土で均し、転倒リスクを解消。
- 作業記録のまとめ
- 現場写真と工程表、点検チェックリストを照合し、報告書用に整理。
- 発生したトラブルや気づき事項を「振り返り欄」に記載し、今後の改善に活かす。
これらの整地・片付け作業を通じて、グランピング施設利用者が快適に過ごせる環境を完全に復旧しました。次節では、施工結果の効果検証と振り返りを行います。
9. 結果と効果検証
- 伐採効果
- 問題樹のシラカシ(樹高約12m)を計4セクションに分割して安全に除去。事前に懸念された倒木リスクは完全に解消され、倒木・落枝の危険がゼロに抑えられました。
- 案内動線上の大木がなくなったことで、ゲストの通行性が向上し、施設入口の視認性も改善しました。
- 作業時間・コスト
- 当初見積もり6時間に対し、実作業は休憩を除いて約5時間30分で完了。余裕を持った工程管理が功を奏しました。
- 人件費・機材費ともに概算予算内に収まり、追加コストは発生していません。
- 安全実績
- 作業中の事故・ヒヤリハットは一切発生せず、全員がフルPPE着用と無線連携を徹底した成果が確認できました。
- 地盤沈下やアウトリガーの不安定もなく、バケット車の安定運用が維持できました。
- 利用者・施設管理者の反応
- 施設管理者からは「想定以上に迅速かつ丁寧な対応だった」と高評価を獲得。利用者からの「木陰がすっきりして見晴らしが良くなった」という声も確認できています。
- 環境への配慮
- 回収した枝幹はチップ化して敷地内の花壇マルチ材や土壌改良材として再利用。廃材処分量を最小限に留めるエコサイクルを実現しました。
以上の結果から、本事例では限られたスペースかつ周辺環境に配慮した上で、安全・迅速・経済的に高木危険伐採を完遂できたと評価します。次節では、得られた気づきと今後の改善ポイントを整理します。
10. 振り返りと今後の改善ポイント
- 事前調査の精度向上
- 樹木内部の腐朽状況を更に正確に把握するため、ドリルテストや赤外線サーモグラフィを活用すると、切断時の想定外の亀裂進行を防ぎやすくなります。
- ロープワークの効率化
- 今回はセクション毎にスリングロープを手動で巻き付けましたが、次回からはクイックアタッチャブルタイプのロープスナッチやプーリーシステムを導入し、作業時間の短縮と腕力依存の軽減を図りたいです。
- アウトリガー設置の標準化
- 地盤状況に応じた支持マットの厚み選定マニュアルを整備し、現場スタッフ全員が迷わず適切なウエハとマットを準備できるようにします。
- 無線システムの予備確保
- 電波干渉やバッテリー切れに備え、ヘルメット内蔵無線機の予備機や長時間バッテリーを導入し、通信トラブルによる作業中断リスクを減らします。
- 環境再生プランの拡充
- 回収枝幹のチップ化再利用だけでなく、伐採跡地に低木や植栽を計画的に配置する「景観保全プラン」を提案し、施設の魅力向上にも繋げたいと考えています。
以上を踏まえ、今後はさらなる安全性と効率性の向上を図りつつ、環境配慮を含めた付加価値の高い伐採サービスを提供してまいります。